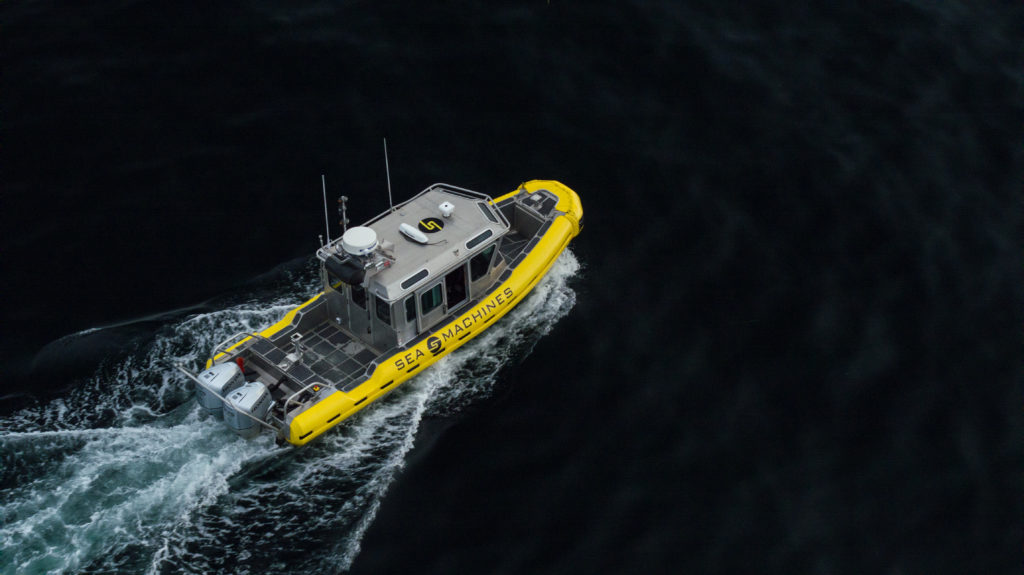
Source: Sea Machines Robotics
BOSTON — Sea Machines Robotics Inc. this week said it has entered into a cooperative agreement with the U.S. Department of Transportation’s Maritime Administration to demonstrate the ability of its autonomous technology in increasing the safety, response time and productivity of marine oil-spill response operations.
Sea Machines was founded in 2015 and claimed to be “the leader in pioneering autonomous control and advanced perception systems for the marine industries.” The company builds software and systems to increase the safety, efficiency, and performance of ships, workboats, and commercial vessels worldwide.
The U.S. Maritime Administration (MARAD) is an agency of the U.S. Department of Transportation that promotes waterborne transportation and its integration with other segments of the transportation system.
Preparing for oil-spill exercise
To make the on-water exercises possible, Sea Machines will install its SM300 autonomous-command system aboard a MARCO skimming vessel owned by Marine Spill Response Corp. (MSRC), a not-for-profit, U.S. Coast Guard-classified oil spill removal organization (OSRO). MSRC was formed with the Marine Preservation Association to offer oil-spill response services in accordance with the Oil Pollution Act of 1990.
Sea Machines plans to train MSRC personnel to operate its system. Then, on Aug. 21, Sea Machines and MSRC will execute simulated oil-spill recovery exercises in the harbor of Portland, Maine, before an audience of government, naval, international, environmental, and industry partners.
The response skimming vessel is manufactured by Seattle-based Kvichak Marine Industries and is equipped with a MARCO filter belt skimmer to recover oil from the surface of the water. This vessel typically operates in coastal or near-shore areas. Once installed, the SM300 will give the MSRC vessel the following new capabilities:
- Remote autonomous control from an onshore location or secondary vessel,
- ENC-based mission planning,
- Autonomous waypoint tracking,
- Autonomous grid line tracking,
- Collaborative autonomy for multi-vessel operations,
- Wireless remote payload control to deploy onboard boom and other response equipment, and
- Obstacle detection and collision avoidance.
Round-the-clock response
In addition, Sea Machines said, it enables minimally manned and unmanned autonomous maritime operations. Such configurations allow operators to respond to spill events 24/7 depending on recovery conditions, even when crews are unavailable or restricted, the company said. These configurations also reduce or eliminate exposure of crewmembers to toxic fumes and other safety hazards.
“Autonomous technology has the power to not only help prevent vessel accidents that can lead to spills, but can also facilitate better preparedness; aid in safer, efficient, and effective cleanup,” said CEO Michael G. Johnson, CEO of Sea Machines. “We look forward to working closely with MARAD and MSRC in these industry-modernizing exercises.”
“Our No. 1 priority is the safety of our personnel at MSRC,” said John Swift, vice president at MSRC. “The ability to use autonomous technology — allowing response operations to continue in an environment where their safety may be at risk — furthers our mission of response preparedness.”
Sea Machines promises rapid ROI for multiple vessels
Sea Machines’ SM Series of products, which includes the SM300 and SM200, provides marine operators a new era of task-driven, computer-guided vessel control, bringing advanced autonomy within reach for small- and large-scale operations. SM products can be installed aboard existing or new-build commercial vessels with return on investment typically seen within a year.
In addition, Sea Machines has received funding from Toyota AI Ventures.
Sea Machines is also a leading developer of advanced perception and navigation assistance technology for a range of vessel types, including container ships. The company is currently testing its perception and situational awareness technology aboard one of A.P. Moller-Maersk’s new-build ice-class container ships.
The post Sea Machines Robotics to demonstrate autonomous spill response appeared first on The Robot Report.