Among the challenges for developers of mobile manipulation and humanoid robots is the need for an affordable and flexible research platform. PAL Robotics last month announced its TIAGo++, a robot that includes two arms with seven degrees of freedom each.
As with PAL Robotics‘ one-armed TIAGo, the new model is based on the Robot Operating System (ROS) and can be expanded with additional sensors and end effectors. TIAGo++ is intended to enable engineers to create applications that include a touchscreen interface for human-robot interaction (HRI) and require simultaneous perception, bilateral manipulation, mobility, and artificial intelligence.
In addition, TIAGo++ supports NVIDIA’s Jetson TX2 as an extra for machine learning and deep learning development. Tutorials for ROS and open-source simulation for TIAGo are available online.
Barcelona, Spain-based PAL, which was named a “Top 10 ROS-based robotics company to watch in 2019,” also makes the Reem and TALOS robots.
Jordi Pagès, product manager of the TIAGo robot at PAL Robotics responded to the following questions about TIAGo++ from The Robot Report:
For the development of TIAGo++, how did you collect feedback from the robotics community?
Pagès: PAL Robotics has a long history in research and development. We have been creating service robotics platforms since 2004. When we started thinking about the TIAGo robot development, we asked researchers from academia and industry which features would they expect or value in a platform for research.
Our goal with TIAGo has always been the same: to deliver a robust platform for research that easily adapts to diverse robotics projects and use cases. That’s why it was key to be in touch with the robotics and AI developers from start.
After delivering the robots, we usually ask for feedback and stay in touch with the research centers to learn about their activities and experiences, and the possible improvements or suggestions they would have. We do the same with the teams that use TIAGo for competitions like RoboCup or the European Robotics League [ERL].
At the same time, TIAGo is used in diverse European-funded projects where end users from different sectors, from healthcare to industry, are involved. This allows us to also learn from their feedback and keep finding new ways in which the platform could be of help in a user-centered way. That’s how we knew that adding a second arm into the TIAGo portfolio of its modular possibilities could be of help to the robotics community.
How long did it take PAL Robotics to develop the two-armed TIAGo++ in comparison with the original model?
Pagès: Our TIAGo platform is very modular and robust, so it took us just few months from taking the decision to having a working TIAGo++ ready to go. The modularity of all our robots and our wide experience developing humanoids usually helps us a lot in reducing the redesign and production time.
The software is also very modular, with extensive use of ROS, the de facto standard robotics middleware. Our customers are able to upgrade, modify, and substitute ROS packages. That way, they can focus their attention on their real research on perception, navigation, manipulation, HRI, and AI.
How high can TIAGo++ go, and what’s its reach?
Pagès: TIAGo++ can reach the floor and up to 1.75m [5.74 ft.] high with each arm, thanks to the combination of its 7 DoF [seven degrees of freedom] arms and its lifting torso. The maximum extension of each arm is 92cm [36.2 in.]. In our experience, this workspace allows TIAGo to work in several environments like domestic, healthcare, and industry.
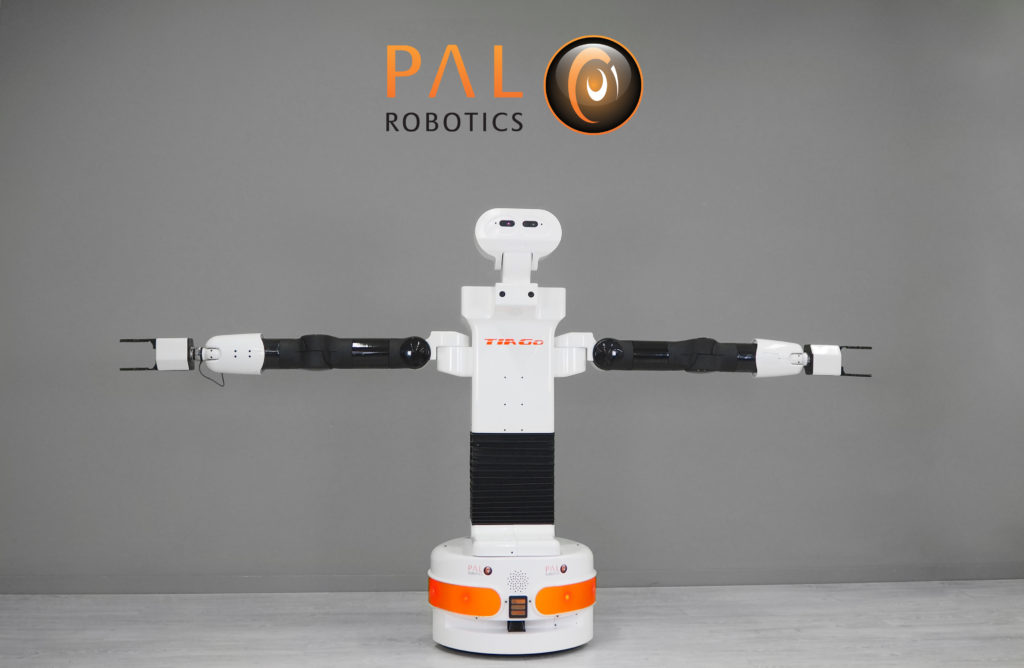
The TIAGo can extend in height, and each arm has a reach of about 3 ft. Source: PAL Robotics
What’s the advantage of seven degrees of freedom for TIAGo’s arms over six degrees?
Pagès: A 7-DoF arm is much better in this sense for people who will be doing manipulation tasks. Adding more DoFs means that the robot can arrive to more poses — positions and orientations — of its arm and end-effector that it couldn’t reach before.
Also, this enables developers to reduce singularities, avoiding non-desired abrupt movements. This means that TIAGo has more possibilities to move its arm and reach a certain pose in space, with a more optimal combination of movements.
What sensors and motors are in the robot? Are they off-the-shelf or custom?
Pagès: All our mobile-based platforms, like the TIAGo robot, combine many sensors. TIAGo has a laser and sonars to move around and localize itself in space, an IMU [inertial measurement unit], and an RGB-D camera in the head. It can have a force/torque sensor on the wrist, especially useful to work in HRI scenarios. It also has a microphone and a speaker.
TIAGo has current sensing in every joint of the arm, enabling a very soft, effortless torque control on each of the arms. The possibility of having an expansion panel with diverse connectors makes it really easy for developers to add even more sensors to it, like a thermal camera or a gripper camera, once they have TIAGo in their labs.
About the motors, TIAGo++ makes use our custom joints integrating high-quality commercial components and our own electronic power management and control. All motors also have encoders to measure the current motor position.
What’s the biggest challenge that a humanoid like TIAGo++ can help with?
Pagès: TIAGo++ can help with are those tasks that require bi-manipulation, in combination with navigation, perception, HRI, or AI. Even though it is true that a one-arm robot can already perform a wide range of tasks, there are many actions in our daily life that require of two arms, or that are more comfortably or quickly done with two arms rather than one.
For example, two arms are good for grasping and carrying a box, carrying a platter, serving liquids, opening a bottle or a jar, folding clothes, or opening a wardrobe while holding an object. In the end, our world and tools have been designed for the average human body, which is with two arms, so TIAGo++ can adapt to that.
As a research platform based on ROS, is there anything that isn’t open-source? Are navigation and manipulation built in or modular?
Pagès: Most software is provided either open-sourced or with headers and dynamic libraries so that customers can develop applications making use of the given APIs or using the corresponding ROS interfaces at runtime.
For example, all the controllers in TIAGo++ are plugins of ros_control, so customers can implement their own controllers following our public tutorials and deploy them on the real robot or in the simulation.
Moreover, users can replace any ROS package by their own packages. This approach is very modular, and even if we provide navigation and manipulation built-in, developers can use their own navigation and manipulation instead of ours.
Did PAL work with NVIDIA on design and interoperability, or is that an example of the flexibility of ROS?
Pagès: It is both an example of how easy is to expand TIAGo with external devices and how easy is to integrate in ROS these devices.
One example of applications that our clients have developed using the NVIDIA Jetson TX2 is the “Bring me a beer” task from the Homer Team [at RoboCup], at the University of Koblenz-Landau. They made a complete application in which TIAGo robot could understand a natural language request, navigate autonomously to the kitchen, open the fridge, recognize and select the requested beer, grasp it, and deliver it back to the person who asked for it.
As a company, we work with multiple partners, but we also believe that our users should be able to have a flexible platform that allows them to easily integrate off-the-shelf solutions they already have.
How much software support is there for human-machine interaction via a touchscreen?
Pagès: The idea behind integrating a touchscreen on TIAGo++ is to bring customers the possibility to implement their own graphical interface, so we provide full access to the device. We work intensively with researchers, and we provide platforms as open as our customers need, such as a haptic interface.
What do robotics developers need to know about safety and security?
Pagès: A list of safety measures and best practices are provided in the Handbook of TIAGo robot in order that customers ensure safety both around the robot and for the robot itself.
TIAGo also features some implicit control modes that help to ensure safety while operation. For example, an effort control mode for the arms is provided so that collisions can be detected and the arm can be set in gravity compensation mode.
Furthermore, the wrist can include a six-axis force/torque sensor providing more accurate feedback about collisions or interactions of the end effector with the environment. This sensor can be also used to increase the safety of the robot. We provide this information to our customers and developers so they are always aware about the safety measures.
Have any TIAGo users moved toward commercialization based on what they’ve learned with PAL’s systems?
Pagès: At the moment, from the TIAGo family, we commercialize the TIAGo Base for intralogistics automation in indoor spaces such as factories or warehouses.
Some configurations of the TIAGo robot have been tested in pilots in healthcare applications. In the EnrichMe H2020 EU Project, the robot gave assistance to old people at home autonomously for up to approximately two months.
In robotics competitions such as the ERL, teams have shown the quite outstanding performance of TIAGo in accomplishing specific actions in a domestic environment. Two teams ended first and third in the RoboCup@Home OPL 2019 in Sydney, Australia. The Homer Team won for the third time in a row using TIAGo — see it clean a toilet here.
The CATIE Robotics Team ended up third in the first world championship in which it participated. For instance, in one task, it took out the trash.
The TIAGo robot is also used for European Union Horizon 2020 experiments in which collaborative robots that combine mobility with manipulation are used in industrial scenarios. This includes projects such as MEMMO for motion generation, Co4Robots for coordination, and RobMoSys for open-source software development.
Besides this research aspect, we have industrial customers that are using TIAGo to improve their manufacturing procedures.
How does TIAGo++ compare with, say, Rethink Robotics’ Baxter?
Pagès: With TIAGo++, besides the platform itself, you also get support, extra advanced software solutions, and assessment from a company that continues to be in the robotics sector since more than 15 years ago. Robots like the TIAGo++ also use our know-how both in software and hardware, a knowledge that the team has been gathering from the development of cutting-edge biped humanoids like the torque-controlled TALOS.
From a technical point of view, TIAGo++ was made very compact to suit environments shared with people such as homes. Baxter was a very nice entry-point platform and was not originally designed to be a mobile manipulator but a fixed one. TIAGo++ can use the same navigation used in our commercial autonomous mobile robot for intralogistics tasks, the TIAGo Base.
Besides, TIAGo++ is a fully customizable robot in all aspects: You can select the options you want in hardware and software, so you get the ideal platform you want to have in your robotics lab. For a mobile manipulator with two 7-DoF arms, force/torque sensors, ROS-based, affordable, and with community support, we believe TIAGo++ should be a very good option.
The TIAGo community is growing around the world, and we are sure that we will see more and more robots helping people in different scenarios very soon.
What’s the price point for TIAGo++?
Pagès: The starting price is around €90,000 [$100,370 U.S.]. It really depends on the configuration, devices, computer power, sensors, and extras that each client can choose for their TIAGo robot, so the price can vary.
The post TIAGo++ robot from PAL Robotics ready for two-armed tasks appeared first on The Robot Report.