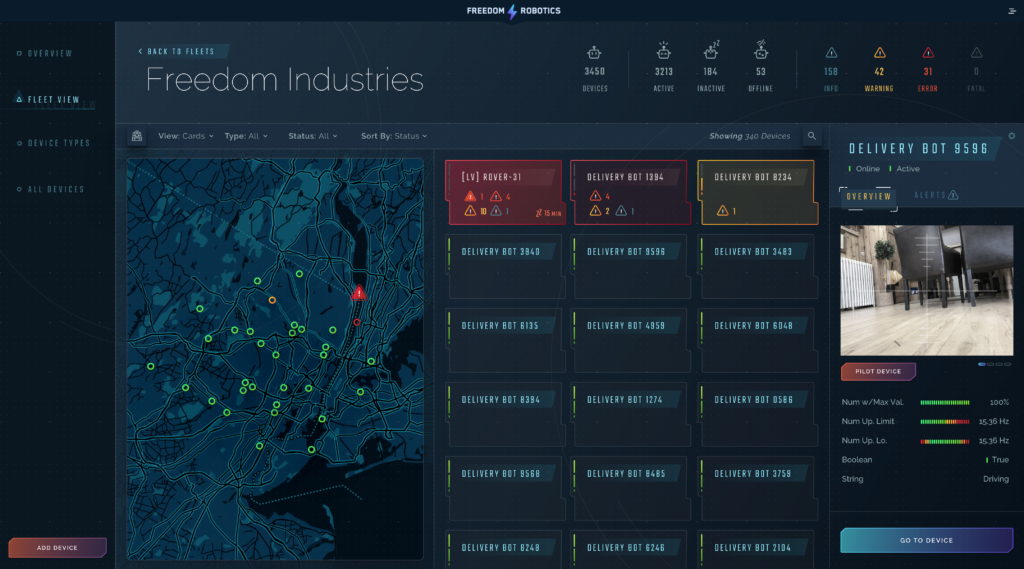
RMS enables fleet management and troubleshooting. Source: Freedom Robotics
SAN FRANCISCO — Freedom Robotics Inc. today announced that it has closed a $6.6 million seed round. The company provides a cloud-based software development infrastructure for managing fleets of robots.
Freedom Robotics cited a study by the World Economic Forum stating that, by 2025, machines will perform more tasks than humans, creating 58 million jobs worldwide. The company plans to use its funding to build its team and technology.
Freedom Robotics claimed that robotics startups can get their products to market 10 times faster by using its tools to do the “undifferentiated heavy lifting” rather than devoting employees to developing a full software stack. The company said its platform-agnostic Robotics Management Software (RMS) provides the “building blocks” for prototyping, building, operating, and scaling robot fleets.
Freedom Robotics builds RMS for developers
“We’ve seen that robotics is hard,” observed Dimitri Onistsuk, co-founder of Freedom Robotics. “In sixth grade, I wrote a letter to myself saying that I would go to MIT, drop out, and found a company that would change the world.”
Onistsuk did go to MIT, drop out, and draw on his experiences with Hans Lee and Joshua Wilson, now chief technology officer and CEO, respectively, at Freedom Robotics.
“We had been building things together before there was a cloud,” recalled Onistsuk. “Now in robotics, very few people have the ability to build a full stack.”
“We see robotics developers who have wonderful applications, like caring for the elderly; transportation; or dull, dirty, and dangerous work,” he said. “Everyone agrees on the value of this area, but they don’t realize the complexity of day-to-day iteration, which requires many engineers and a lot of infrastructure for support.”
“Robotics is like the Web in 2002, where everyone who wants to make an attempt has to raise $10 million and get expert talent in things like computer vision, mechatronics, systems integration, and ROS,” Onistsuk told The Robot Report. “It costs a lot of money to try even once to get a product to market.”
“We’ve combined layers of distinct software services by bringing modern software-development techniques into robotics, which traditionally had a hardware focus,” he said. “You can use one or many — whatever you have to do to scale.”
‘AWS for robots’
Freedom Robotics said that its cloud-based tools can be installed with just a single line of code, and its real-time visualization tools combine robotics management and analysis capabilities that were previously scattered across systems.
“Developers are always trying to improve their processes and learn new things,” said Onistsuk. “Amazon Web Services allows you to bring up a computer with a single line of code. We spent most of the first six months as a company figuring out how to do that for robots. We even bought the domain name ’90 seconds to go.'”
“You can drop in one line of code and immediately see real-time telemetry and have a cloud link to a robot from anywhere in the world,” he said. “Normally, when you want to adopt new components and are just trying to build a robot where the components talk to one another, that can take months.”
“During one on-boarding call, a customer was able to see within two minutes real-time telemetry from robots,” Onistsuk said. “They had never seen sensor-log and live-streaming data together. They thought the video was stuttering, but then an engineer noticed an error in a robot running production software. The bug had already been pushed out to customers. They never had the tools before to see all data in one place in developer-friendly ways.”
“That is the experience we’re getting when building software alongside the people who build robots,” he said. “With faster feedback loops, companies can iterate 10 times faster and move developers to other projects.”
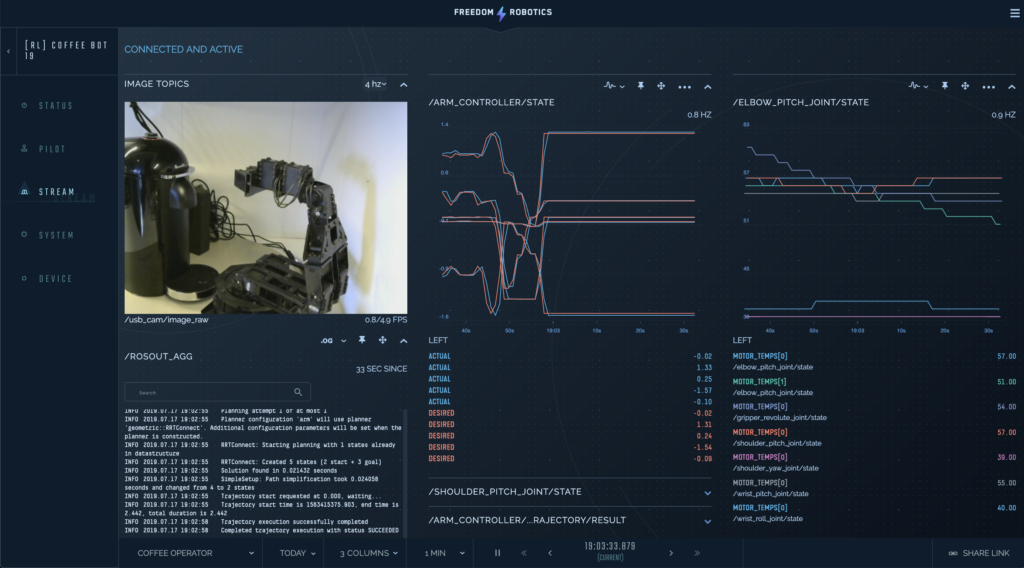
Freedom Robotics’ RMS combines robotics tools to help developers and robotics managers. Source: Freedom Robotics
The same tools for development, management
Onistsuk said that his and Lee’s experience led them to follow standard software-development practices. “Some truths are real — for your core infrastructure, you shouldn’t have to own computers — our software is cloud-based for that reason,” he said.
“We stand on the shoulders of giants and practice what we preach,” Onistsuk asserted. “Pieces of our underlying infrastructure run on standard clouds, and we follow standard ways of building them.”
He said that not only does Freedom Robotics offer standardized development tools; it also uses them to build its RMS.
“With a little thought, for anything that you want to do with our product, you have access to the API calls across the entire fleet,” said Onistsuk. “We used the same APIs to build the product as you would use to run it.”

Resource monitoring with RMS. Source: Freedom Robotics
Investors and interoperability
Initialized Capital led the funding round, with participation from Toyota AI Ventures, Green Cow Venture Capital, Joe Montana’s Liquid 2 Ventures, S28 Capital partner Andrew Miklas, and James Lindenbaum. They joined existing investors Kevin Mahaffey, Justin Kan, Matt Brezina, Arianna Simpson, and Josh Buckley.
“We’ll soon reach a point when there are more robots than cell phones, and we’ll need the ‘Microsoft of robotics’ platform to power such a massive market,” said Garry Tan, managing partner at Initialized Capital, which has backed companies such as Instacart, Coinbase, and Cruise.
“Cloud learning will be a game-changer for robotics, allowing the experience of one robot to be ‘taught’ to the rest on the network. We’ve been looking for startups with the technology and market savvy to realize this cloud robotics future through fleet management, control, and analytics,” said Jim Adler, founding managing director at Toyota AI Ventures. “We were impressed with Freedom Robotics’ customer-first, comprehensive approach to managing and controlling fleets of robots and look forward to supporting the Freedom team as they make cloud robotics a market reality.”
“We found out about Toyota AI Ventures through its Twitter account,” said Onistsuk. “We got some referrals and went and met with them. As the founder of multiple companies, Jim [Adler] understood us in a way that industry-specific VCs couldn’t. He got our experience in robotics, building teams, and data analytics.”
What about competing robotics development platforms? “We realized from Day 1 that we shouldn’t be fighting,” Onistsuk replied. “We’re fully integrated with the cloud offerings of Amazon, Google, and Microsoft, as well as ROS. We have drop-in compatibility.”
“What we’re trying to power with that is allowing developers to build things that differentiate their products and services and win customers,” he added. “This is similar to our cloud-based strategy. We try to be hardware-agnostic. We want RMS to work out of the box with as many tools and pieces of hardware as possible so that people can try things rapidly.”

The Freedom Robotics team has raised seed funding. Source: Freedom Robotics
Hardware gets commoditized
“Hardware is getting commoditized and driving market opportunity,” said Onistsuk. “For instance, desktop compute is only $100 — not just Raspberry Pi, but x86 — you can buy a real computer running a full operating system.”
“Sensors are getting cheaper thanks to phones, and 3D printing will affect actuators. NVIDIA is putting AI into a small, low-power form factor,” he added. “With cheaper components, we’re looking for $5,000 robot arms rather than $500,000 arms, and lots of delivery companies are looking to make a vehicle autonomous and operating at a price point that’s competitive.”
“Companies can use RMS to build their next robots as a service [RaaS], and we’ve worked with everything from the largest entertainment companies to sidewalk delivery startups and multibillion-dollar delivery companies,” Onistsuk said. “Freedom Robotics is about democratizing robotics development and removing barriers to entry so that two guys in a garage can scale out to a business because of demand. The dreams of people with real needs in robotics will cause the next wave of innovation.”
“Software infrastructure is hard to do — we take what many developers consider boring so that they can sell robots into businesses or the home that get better over time,” he said.

‘Inspiring’ feedback
Customer feedback so far has been “overwhelmingly inspiring,” said Onistsuk. “The best moments are getting an e-mail from a customer saying, ‘We’re using your product, and we thought we didn’t want some login or alerting plug-in. We have a demo tomorrow, and it would take four months to build it, but you can do it.'”
“We’ve seen from our interactions that the latest generation of robotics developers has different expectations,” he said. “We’re seeing them ‘skating to where the puck is,’ iterating quickly to build tools and services around our roadmap.”
“The RMS is not just used by developers,” Onistsuk said. “Development, operations, and business teams can find and solve problems in a collaborative way with the visualization tool. We can support teams managing multiple robots with just a tablet, and it integrates with Slack.”
“We can go from high-level data down to CPU utilization,” Lee said. “With one click, you can get a replay of GPS and telemetry data and see every robot with an error. Each section is usually one engineer’s responsibility.”
“A lot of times, people develop robots for university research or an application, but how does the robot perform in the field when it’s in a ditch?” said Lee. “We can enable developers to make sure robots perform better and safer.”
Freedom Robotics is currently being used in industries including agriculture, manufacturing, logistics, and restaurants, among others.
“This is similar to getting dev done in minutes, not months, and it could speed up the entire robotics industry,” Onistsuk added. “Investors are just as excited about the team, scaling the business, and new customers as I am.”
The post Freedom Robotics raises seed funding for robotics dev tools, fleet controls appeared first on The Robot Report.