Top 10 robotic stories of May 2022
May was full of exciting developments in the robotics world. From NASA nearing the retirement of its InSight Lander, to IP acquisitions, to Festo introducing a pneumatic cobot arm, there was no shortage of things to cover this month.
Here are the Top 10 most popular robotics stories on The Robot Report in May 2022. Subscribe to The Robot Report Newsletter to stay updated on the robotics stories you need to know about.
10. 3 leading US robotics clusters create alliance
MassRobotics, Pittsburgh Robotics Network and Silicon Valley Robotics have formed the United States Alliance of Robotics Clusters (USARC). USARC supports the development, commercialization and scaling of robotics for global good by collaborating with government and industry stakeholders. Read More
9. Mercedes rolls out Level 3 autonomous driving tech in Germany
Mercedes-Benz launched sales of its Drive Pilot system in Germany. The system is capable of operating at SAE Level 3 autonomy and can be ordered for the company’s S-Class and all-electric EQS models. Mercedes’ system was approved by the German Federal Motor Transport Authority (KBA) for Level 3 autonomy in December 2021. The approval allows Drive Pilot to take over driving in certain areas and at speeds of up to 60 km/h, around 37 mph, as long as someone is in the driver’s seat and prepared to take control of the vehicle at any time. Read More
8. Qualcomm unveils RB6 platform and RB5 AMR reference design
Qualcomm announced the availability of its Robotics RB6 Platform and the RB5 Reference Design. The two products help to bring advanced artificial intelligence (AI) and 5G to robotics, drones and intelligence machines. The RB6 Platform is made up of both hardware and software development tools. Read More
7. Boston Dynamics upgrades Spot with faster charging, new payloads, 5G
Boston Dynamics announced the latest upgrades for its popular quadruped robot Spot. The upgrades include faster charging times, more payloads and support for 5G connectivity. Boston Dynamics has added additional payloads to the quadruped to help it operate in more areas. The Spot CORE I/O is a high-efficiency computer payload that gives Spot the ability to process data in the field. Read More
6. Verizon shutting down Skyward drone management company
Skyward, a drone management company owned by Verizon, is shutting down. The company’s drone software platform helped customers manage their entire drone workflow, including training crews, planning missions, accessing controlled airspace and more. Skyward began in 2013 in Portland, Oregon, and was acquired by Verizon in 2017. Read More
5. Savioke is now Relay Robotics
Relay Robotics launched. It is a new corporation formed by acquiring Savioke, a developer of mobile delivery robots. The people, intellectual property, the Relay product line, and all customer agreements have all come over to Relay Robotics. Relay Robotics also announced the completion of a $10M Series A financing and the appointment of veteran technology executive Michael O’Donnell as chairman and CEO. Read More
4. Festo introduces pneumatic cobot arm
Festo announced its pneumatic collaborative robot (cobot) arm at the Festo TechTalk 2022. The company plans to make the cobot commercially available in 2023. The cobot uses six pneumatic direct drives, instead of the typical electric motors and mechanical transmission, to move. Each of the six drives consists of a circular chamber with a moveable partition. Differences in air pressure on either side of the partition wall in the chamber cause the it to shift, which then moves the joint. Read More
3. DeepMind’s open-source version of MuJoCo available on GitHub
DeepMind, an AI research lab and subsidiary of Alphabet, in October 2021 acquired the MuJoCo physics engine for robotics research and development. The plan was to open-source the simulator and maintain it as a free, open-source, community-driven project. According to DeepMind, the open sourcing is now complete, and the entire codebase is on GitHub. Read More
2. John Deere acquires camera-based perception tech from Light
John Deere has made another acquisition related to the development of autonomous tractors. John Deere has acquired numerous patents and other intellectual property from Light, which specializes in depth sensing and camera-based perception for autonomous vehicles. John Deere also hired a team of employees from Light. Financial terms of the deal are unknown. Read More
1. NASA’s InSight Lander nearing end of journey on Mars
NASA’s InSight Lander touched down on the surface of Mars on November 26, 2018 after a six-month journey from Earth. NASA’s primary goal for the lander was to glean a better understanding of how terrestrial planets, like Earth and Mars, formed and evolved. Over three years later, InSight has achieved all of its primary science goals. Read More
The post Top 10 robotic stories of May 2022 appeared first on The Robot Report.
Introducing GTGraffiti: The robot that paints like a human
An approach to produce elaborate flying maneuvers using morphing-wing drones
Shape-shifting drone flies and dives to find aquatic environmental clues
How 5G connectivity can enhance AMRs
While there is significant consumer interest around 5G for improved mobile device performance, there is also a great need among industrial companies to implement the technology within their facilities. This is because the demand for innovation and digitalization of factories has never been greater. When it comes to improving material flow, which in turn reduces machine idle time and other disruptions, the use of autonomous mobile robots (AMRs) in conjunction with other computing and connectivity technologies is often the best solution.
Indeed, the increasing size of AMR fleets and the expanding use of Industry 4.0 and industrial internet of things (IIoT) technologies on the shop floor is driving the need to adopt industrial-grade 5G private wireless communications. This upgrade to a more capable communications technology is needed to handle the increased networking loads with reliable, low-latency connectivity.
For efficient processes and operations, it is crucial that AMRs get the right job assignment at the right time, can perform the task when it is expected, and coordinate well with other AMRs and site conditions. High-speed and reliable connectivity is required to perform these and other tasks. For these reasons, industry leaders in the fields of AMRs and 5G wireless are teaming up to roll out the coordinated use of these technologies in the field.
AMRs in action
Material transport within facilities was often a manual or semi-automated process, with limited flexibility. For many years, AMRs have been applied to improve upon this situation by delivering reliable material transport in facilities while improving worker safety. AMRs directly improve overall equipment effectiveness (OEE) by reducing machine idle time waiting for materials. They also minimize the need for people to perform mundane, repetitive, and unwieldy tasks.
Although AMRs do operate independently to an extent, they must also safely work in close proximity to people, equipment, and other industrial vehicles, which requires them to navigate and coordinate intelligently (Figure 1). On-board sensors do part of the work, but much of the interaction is through wireless communications to a fleet management system. To fully unlock operational value, an efficient and well-planned AMR fleet also needs to be extremely flexible to meet varying demands. Used correctly, the typical AMR ROI is less than 24 months.

Figure 1: AMRs like the OMRON model shown need reliable wireless communications so they can safely and efficiently navigate and coordinate with people, equipment, and other industrial vehicles. | Credit: OMRON
Today’s AMRs work well with Wi-Fi, but there are many compelling reasons why local on-site 5G connectivity improves AMR performance. In some cases, AMRs are implemented over existing Wi-Fi systems already used for business and other IIoT purposes, limiting network performance. Other newer AMR capabilities are compounding the need for increased bandwidth and better response times:
- Addition deeper application automation, progressing from semi- to fully-automated
- Multi-sensor fusion frameworks, such as inspection cameras on and off board
- High-mix, low-volume material traceability
As Wi-Fi networks become loaded—and overloaded—when used for too many purposes, they may remain adequate for non-critical applications, but real-time functionality will suffer. Some users bump into Wi-Fi challenges like:
- Limited/spotty coverage
- Undependable handoffs between access points
- Declining bandwidth
- Unpredictable latency
- Insufficient cybersecurity
While a small AMR fleet may work fine with Wi-Fi, any increase in size, functionality, and loading typically requires a dedicated network solution for these mission critical applications. Successful and scalable AMR deployments need predictable network performance to enable improved OEE and deliver a faster ROI.
5G advantages
Wi-Fi is very IT-centric and was not conceived to operate in the most challenging environments. Nokia has been providing 2G (GSM), 3G (UMTS), 4G (LTE), and 5G cellular networks to both communication service providers and enterprises and is the global leader in private wireless networks. While the requirements from the first generations in mobile communication were mainly driven by service providers focused on consumer needs, the story has changed with 5G.
Industrial automation companies have contributed on defining the requirements for the 5G standards, based on the needs from OT. Furthermore, companies like OMRON and Nokia have entered into strategic partnerships to accelerate the use of 5G solutions in the industrial sector, helping the move to Industry 4.0. The 5G technology improves on many areas where Wi-Fi can falter, and it is estimated to deliver a 25% performance improvement in terms of availability and optimization for real-time manufacturing environments (Figure 2).
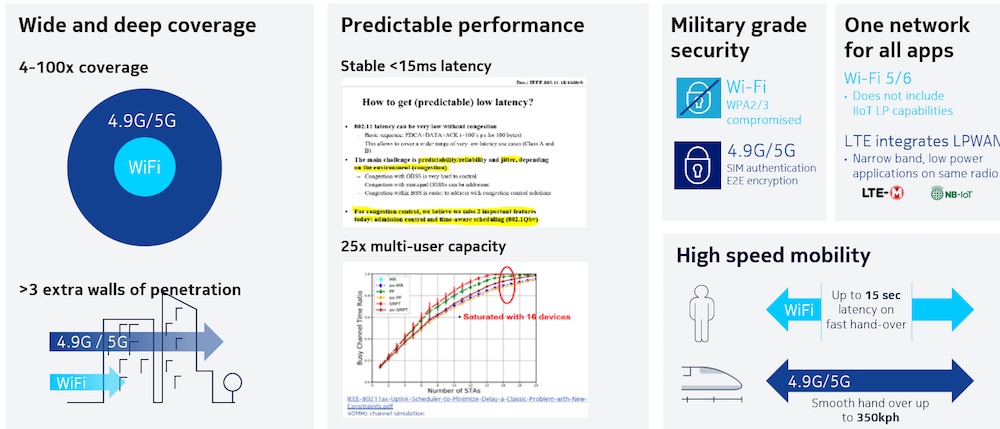
Figure 2: Nokia is an industry leader in developing 5G technologies that outperform Wi-Fi in all aspects. | Credit: OMRON
The 5G is rolling out in phases, and the cornerstones are based on optimizing the following aspects in all environments, including industrial (Figure 3):
- Bandwidth
- Latency and reliability
- Massive IoT connectivity
One example of industrial engagement is 5G support for crucial aspects such as time sensitive networking (TSN), which ensures critical communications are transacted in under 1 ms. Other top 5G performance features applicable to industrial applications include:
- Capacity: can handle 1 million connected devices per square kilometer
- Indoor coverage: typically a 20-60 meter access point radius able to penetrate multiple building walls
- Quality of Service (QoS): Traffic management with prioritization
- Performance: Predictable data rates, with six-9’s reliability
- Mobility: Devices can move at speeds up to 500 km/hr
- Latency: 1-10 ms, remaining stable even with more connections supporting TSN
- Security: Zero-trust design with military-grade security through authentication and end-to-end encryption
- Services: One network handles all voice, broadband, video, IoT, and TSN traffic
- Interference: Ability to use dedicated spectrum
- Network slicing: For segregating traffic
- Geo-positioning: Targeting up to 20 cm accuracy
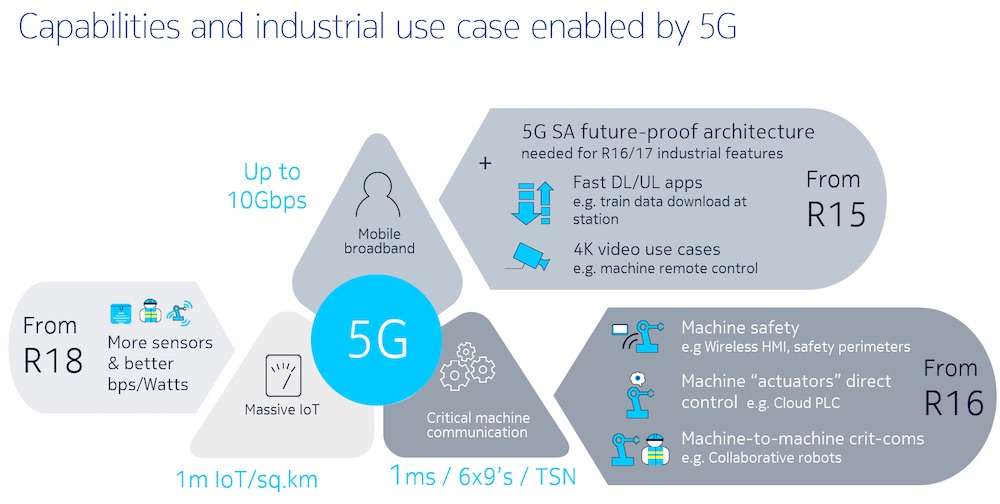
Figure 3: 5G technologies are developed to address the needs of consumers, commercial users, and industrial applications in terms of bandwidth, latency, reliability and massive IoT connectivity. | Credit: OMRON
While Wi-Fi operates on an open spectrum susceptible to interference, 5G is a frequency-licensed technology. Users can deploy their own scaled-down 5G network localized on a site, or they can work with a communication service provider who dedicates slices of the public network for a specified end user. For most industrial applications, the private wireless network approach would be preferred for security, performance, and reliability.
On 5G networks, the handoff of a device from one access point to another is very smooth because 5G devices are constantly communicating with multiple access points and the handoff decision is centrally controlled. This results in an improved performance compared to WiFi, especially when it comes to packet losses and interruption on the communication when the device is moving.
Wi-Fi often has problems with certain physical signal barriers, whereas 5G benefits from reflections caused by the large quantity of metal typically found in industrial environments (Figure 4).
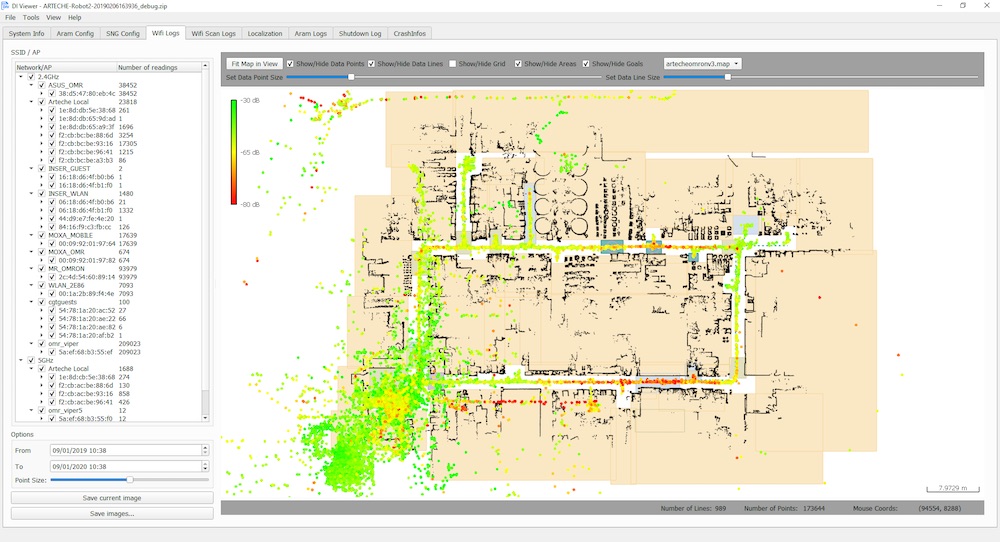
Figure 4: This heat map showing AMRs with respect to Wi-Fi signal strength is representative of the analysis tools developed because coverage is so important for deployments. Private 5G overcomes a variety of problems so AMR fleets run more effectively. | Credit: OMRON
For all these and other reasons, there is significant industry interest in applying 5G for many types of industrial applications. At many locations, existing Wi-Fi infrastructure is proving insufficient, so the build-out using new technology may already be under way or imminent.
AMRs and 5G – better together
AMRs generally demand better than 100ms latency between the AMR and the fleet manager. While some existing technologies can do this, none can do so with all the other benefits provided by 5G. AMRs communicate with supervisory systems to send (upload) and receive (download) data and information like:
- Download configuration/map changes
- Upload activity data
- Upload image/camera information
- Upload/download navigation/coordination information
Some of these activities are constant low-latency/low-bandwidth, while others are intermittent high-bandwidth where latency is less critical. With current technologies, users must be aware of these needs and balance activity to avoid streaming too much data or performing too many changes at once so there will be no momentary overloads. High latency can lead to trajectory information being shared too late for the AMR to make an appropriate steering decision, causing less than intelligent behavior. In the best case users would only experience a slowdown in cycle times, but in the worst case a collision could occur.
To overcome these challenges, OMRON and Nokia are working globally to install 5G in both development and production facilities to capture detailed data for future product development. Deployments of 5G for connecting AMRs have been evaluated and are in production at the OMRON Kusatsu factory and the Nokia Oulu factory.
One rollout is for a large industrial manufacturer, which wants to deploy 5G technology at 250 manufacturing plants worldwide. They are becoming acquainted with the technology and training their IT team because they want to operate and manage their 5G private network themselves.
End users of any size can benefit from 5G private wireless because it’s possible to install and run small-scale plug-and-play solutions, along with larger and more robust platform options. It is also possible for independent systems integrators (SIs) to deploy, operate, and maintain on-site 5G networks for their clients. Another option is for a large telecom operator to offer 5G services to localized end users as a slice of the public network, or as a private wireless network, leveraging their own frequency spectrum.
AMRs using 5G will accelerate applications
AMRs are helping companies everywhere work more efficiently and safely. As digital transformation and IoT initiatives progress, it is natural for users to incorporate advanced data gathering, visualization, and fleet management tasks into their AMRs. In many cases, however, the existing WiFi infrastructure constrains this growth.
For industrial operations, 5G private wireless networks delivers the high bandwidth, reliable low-latency connectivity, and massive IoT capabilities to meet the needs of current and future AMR deployments. 5G is becoming mainstream for commercial use, and there are many options for integrating it into industrial environments. OMRON and Nokia are leaders in AMR and 5G technology, and the two companies are working together to deliver field-proven solutions.
The post How 5G connectivity can enhance AMRs appeared first on The Robot Report.
Field Robotics Engineering Forum call for speakers open
WTWH Media invites you to submit a session abstract to be considered for presentation at the Field Robotics Engineering Forum, to be held October 19-20, 2022 at the Santa Clara Convention Center, Santa Clara, CA.
The Field Robotics Engineering Forum is an international conference and exposition specifically designed to provide engineers, engineering management, business professionals and others, with the information, guidance and peer networking opportunities they need to successfully develop and safely deploy the next generation of robotics systems for operation in wide-ranging, outdoor, dynamic environments.
The Field Robotics Engineering Forum is seeking thought-provoking sessions delivered by compelling speakers in each of the four tracks listed below:
- Technologies, Tools and Platforms Track – Sessions in the Technologies, Tools and Platforms will cover the latest advances in the ‘core’ technologies common to all classes of field robotics systems that allow them to “Sense, Think and Act”.
- Development, Testing and Deployment Track – Topics covered in the Development, Testing and Deployment Track focus on robotics design, development, and testing tools, as well as standards and methodologies, that speed and ease the development and deployment of field robotics systems.
- Markets and Applications Track – Sessions in the Markets and Applications Track focus on those industry and application specific attributes unique to specific field robotics systems, with sessions providing insights and recommendations into the optimal design, development and deployment choice for specific system classes.
Submission form
Deadline
The entry deadline for submitting speaker proposals is June 30, 2022.
All speakers receive
- Complimentary full registration
- Admission to all keynotes, general sessions, panels, special events, breakfasts, lunches and receptions
- Complimentary guest registrations up to two attendees
Co-located events
The Field Robotics Engineering Forum will be co-located with the RoboBusiness, an international conference and exposition designed to provide engineers, engineering management, business professionals and others, with the information, guidance and peer networking opportunities they require to successfully develop and safely deploy the next generation of field robotics systems for operation in wide-ranging, outdoor, dynamic environments.
Also co-located with RoboBusiness is DeviceTalks West, the premier industry event for medical technology professionals, currently in its ninth year. Both events attract engineering and business professionals from a broad range of healthcare and medical technology backgrounds.
Sponsorship opportunities
For information about sponsorship and exhibition opportunities, download the prospectus. Question regarding sponsorship opportunities should be directed to Courtney Nagle at cnagle[AT]wtwhmedia.com.
Conference programming
For questions regarding RoboBusiness Conference & Expo conference programming, contact Dan Kara at dkara[AT]wtwhmedia.com.
About WTWH Media
WTWH Media is an integrated media company serving engineering, business and investment professionals through 50+ websites, 5 print publications, along with many other technical and business events. WTWH’s Robotics Group produces The Robot Report, Robotics Business Review, Collaborative Robotics Trends and Mobile Robot Guide, online technical, business and investment news and information portals focused on robotics and intelligent systems. WTWH Media also produces leading in-person robotics conferences including the Robotics Summit & Expo, RoboBusiness the Field Robotics Engineering Forum and the Healthcare Robotics Engineering Forum. See www.wtwhmedia.com for more information.
The post Field Robotics Engineering Forum call for speakers open appeared first on The Robot Report.
Watch Ghost Robotics’ quadruped go swimming
Ghost Robotics’ Vision 60 quadruped robot can now swim. The Vision 60 can be fully amphibiou when equipped with Onyx Industries’ Nautical Autonomous Unmanned Tail (NAUT).
According to Ghost Robotics, adding NAUT makes Vision 60 the first fully amphibious quadruped. While others have been made waterproof so they can walk through shallow water, Vision 60 is the first to actually swim in water.
Check out our Vision 60 swimming! Thanks to the talented team at Onyx Industries for creating the Nautical Autonomous Unmanned Tail (NAUT) for us. #defensetechnology #robotics #ugv #teamwork pic.twitter.com/B1Ek4y7fq3
— Ghost Robotics (@Ghost_Robotics) June 13, 2022
Onyx’s NAUT jet propulsion unit can propel a robot at up to 3 knots for around 25 minutes on a single charge, according to reporting from The Drive. The unit operates with Onyx’s proprietary autonomous propulsion method and is plug-and-play for integration into existing networks.
NAUT includes a semi-autonomous control system that allows an operator to control the robot remotely or have it execute pre-programed missions autonomously. According to Onyx, NAUT can be added to any IP67 or above rated platform.
Vision 60 is a mid-sized, high-endurance quadruped intended for use in defense, homeland and enterprise applications. The robot is agile and durable enough to survive all-weather conditions in a wide range of environments. The quadruped can walk at up to 3 m/s and run for three hours or travel 10 km on a single charge.
Ghost Robotics has shipped over 200 Vision 60 robots or over 25 national security customers, among others. The company was founded in 2015 by Avik De, Gavin Kenneally and Jiren Parikh.
Onyx and Ghost Robotics unveiled the collaboration at the 2022 Special Operations Forces Industry Conference.
The post Watch Ghost Robotics’ quadruped go swimming appeared first on The Robot Report.
Ubuntu Core 22 now supports real-time compute for robotics
Canonical today announced that Ubuntu Core 22, the fully containerized Ubuntu 22.04 LTS variant optimized for IoT and edge devices, is now generally available for download. This release brings Ubuntu’s operating system (OS) and services to a complete range of embedded and IoT devices.
“Our goal at Canonical is to provide secure, reliable open source everywhere – from the development environment to the cloud, down to the edge and to devices,” said Mark Shuttleworth, CEO of Canonical. “With this release, and Ubuntu’s real-time kernel, we are ready to expand the benefits of Ubuntu Core across the entire embedded world.”
Real-time compute support
The Ubuntu 22.04 LTS real-time kernel, now available in beta, delivers high performance, low latency and workload predictability for time-sensitive industrial, telco, automotive and robotics use cases.
The new release includes a fully preemptible kernel to ensure time-bound responses. Canonical partners with silicon and hardware manufacturers to enable advanced real-time features out of the box on Ubuntu Certified Hardware.
Application-centric
Ubuntu Core provides a fully containerized Ubuntu, which breaks down the monolithic Ubuntu image into packages known as snaps – including the kernel, OS and applications. Each snap has an isolated sandbox that includes the application’s dependencies, to make it fully portable and reliable. Canonical’s Snapcraft framework enables on-rails snap development for rapid iteration, automated testing and reliable deployment.
The system offers transactional mission-critical over-the-air (OTA) updates of the kernel, OS and applications – updates will always complete successfully, or roll back automatically to the previous working version, so a device cannot be “bricked ” by an incomplete update. Snaps also provide delta updates to minimise network traffic, and digital signatures to ensure software integrity and provenance.
Ubuntu Core also provides advanced security features out of the box, including secure boot, full disk encryption, secure recovery and strict confinement of the OS and applications.
Customers benefit from Canonical’s 10 years security maintenance of kernel, OS and application-level code, enabling devices and their applications to meet enterprise and public sector requirements for digital safety.
Partner ecosystem
Partnerships with leading silicon and hardware partners, including Advantech, Lenovo and many others, have established Ubuntu Core’s presence in the market.
The Ubuntu Certified Hardware program defines a range of off-the-shelf IoT and edge devices trusted to work with Ubuntu. The program uniquely includes continuous testing of certified hardware at Canonical’s labs with every security update over the full lifecycle of the device.
“Advantech provides embedded, industrial, IoT and automation solutions. We continue to strengthen our participation in the Ubuntu Certified Hardware Program. Canonical ensures that certified hardware goes through an extensive testing process and provides a stable, secure, and optimized Ubuntu Core to reduce time to market and development costs for our customers.” said Eric Kao, Director of Advantech WISE-Edge+.
The post Ubuntu Core 22 now supports real-time compute for robotics appeared first on The Robot Report.